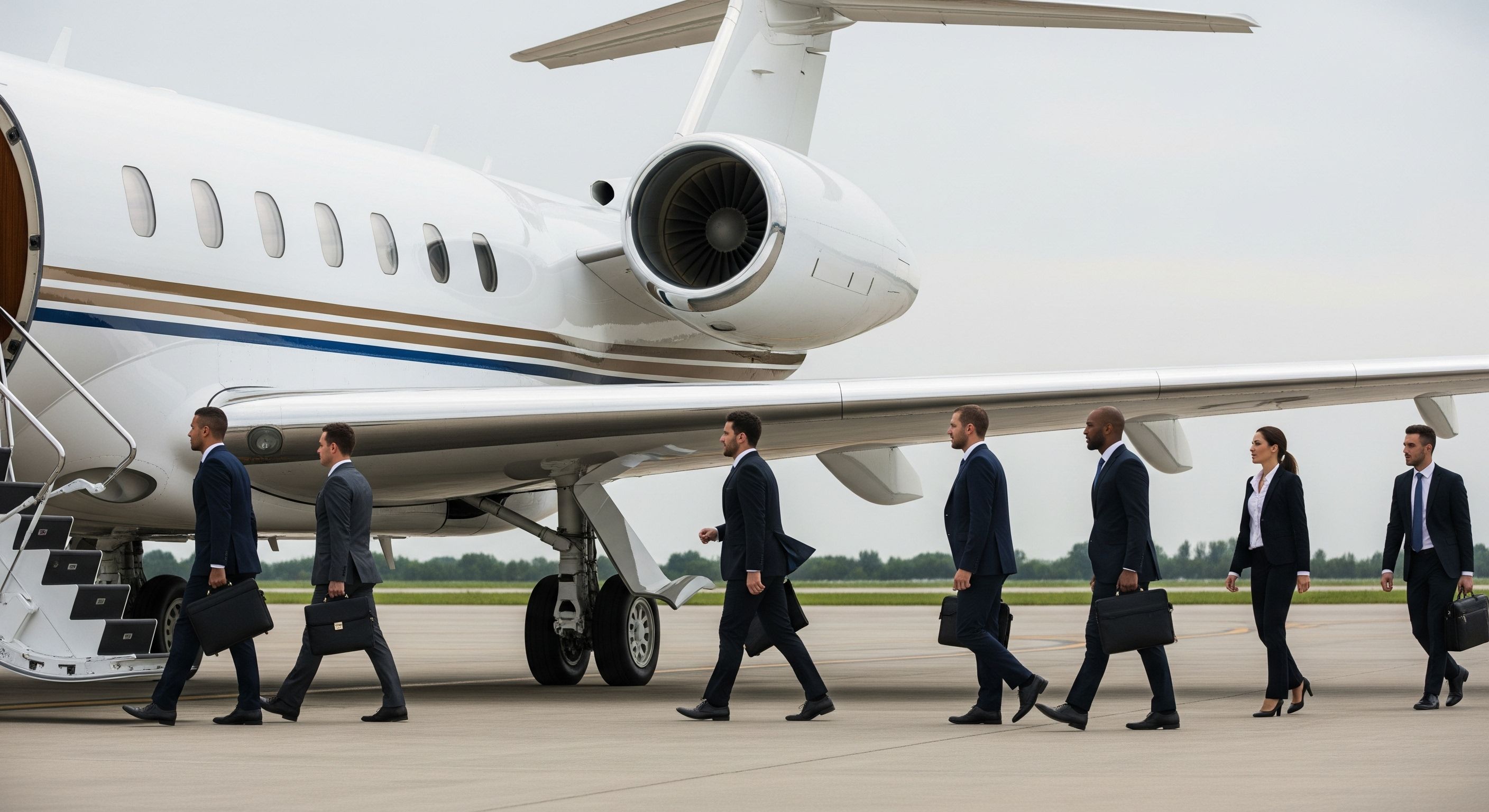
Insights & News
Wing loading definition, effects and design
Published Friday, July 18, 2025
Wing loading is a critical concept in aircraft design that significantly impacts an airplane's performance, efficiency, and handling characteristics. This article provides a comprehensive guide to understanding wing loading, including its definition, calculation, and effects on various aspects of flight.
What is wing loading?
Definition of wing loading
Wing loading is the total weight of an aircraft divided by the area of its wing. The higher the aircraft's weight and the smaller its wing area, the higher the wing loading. Conversely, an aircraft with a lower weight and a larger wing area will have a lower wing loading.
This ratio of weight to wing area has important consequences on the aircraft's performance. A higher wing loading generally results in an aircraft that must fly at higher speeds to generate enough lift. It will take longer distances to take off and land. However, a high wing loading also allows an aircraft to fly faster and be less affected by turbulence and wind gusts.
Calculating wing loading
Wing loading is the total weight of an aircraft divided by the area of its wing. The formula is straightforward:
Wing Loading = Weight / Wing Area
For example, let's calculate the wing loading of a small general aviation aircraft with a maximum takeoff weight of 2,500 lbs and a wing area of 160 sq ft.
Wing Loading = 2,500 lbs / 160 sq ft = 15.6 lbs/sq ft
This means each square foot of wing must generate 15.6 lbs of lift at takeoff to get the aircraft airborne. A higher number like this indicates a relatively heavily loaded aircraft that will require more airspeed to take off and land.
Effects of wing loading on aircraft performance
Takeoff and landing performance
Higher wing loading has a significant impact on an aircraft's takeoff and landing performance. With a greater ratio of weight to wing area, an airplane requires higher airspeeds to generate sufficient lift during these critical phases of flight.
This translates to longer takeoff rolls and landing distances. An aircraft with high wing loading must accelerate to a greater speed before it can lift off, using more runway in the process. On landing, it will maintain a higher approach speed and touch down at a faster rate, again needing more distance to come to a stop.
For example, compare a Cessna 172 with a wing loading of about 15 lb/ft2 to an F-16 fighter at around 90 lb/ft2. The Cessna can take off and land in under 1000 ft, while the F-16 requires over 3000 ft even with its more sophisticated high-lift devices and braking systems. That extra speed and distance is the price paid for the F-16's superior high-speed performance enabled by its high wing loading.
Cruise speed and efficiency
Higher wing loadings enable aircraft to fly faster during cruise. With a greater weight relative to wing area, the wings generate more lift at a given speed. This allows the plane to fly at higher velocities while maintaining level flight.
However, this speed comes with a trade-off in efficiency. The extra lift required at cruise means the wings are working harder, creating more induced drag. This increases the thrust required from the engines, burning more fuel. Range and endurance can suffer as a result.
Maneuverability and stability
Wing loading has a significant impact on an aircraft's maneuverability and stability. Low wing loading, which means a larger wing area relative to the aircraft's weight, allows for tighter turns and greater agility in the air. The extra lift generated by the wings gives the aircraft more responsiveness to control inputs and the ability to change direction quickly.
High wing loading produces the opposite effects. A smaller wing relative to the aircraft's weight reduces maneuverability, as there is less lift available to enable sharp turns and rapid changes of direction. But this configuration provides greater stability, as the wings are less affected by turbulence. High wing loading aircraft tend to fly smoother in rough air and maintain their trajectory with less pilot effort.
Wing loading considerations in aircraft design
Fighter jets and high-speed aircraft
Fighter jets like the F-16 are designed for high speed and maneuverability. To achieve this, they have:
- High wing loading, meaning a smaller wing area relative to their weight. This allows them to fly faster, as each unit of wing area generates more lift at high speeds.
- Powerful engines with low power loading (high thrust-to-weight ratio). The F-16's F110-GE-129 turbofan produces 29,000 lbf of thrust, giving a thrust-to-weight ratio over 1:1. This provides the acceleration and climb performance needed for combat.
Transport and commercial aircraft
Efficiency is paramount for airliners, which aim to carry heavy payloads long distances at the lowest possible cost. However, designers must balance efficiency against other important factors like runway performance, cruise speed, and passenger comfort. Wing loading is a key consideration in striking the right compromise.
Airliners typically have moderate wing loading in the range of 500-700 kg/m2 (102-143 lb/ft2). This is much higher than light aircraft, but significantly lower than high-performance military jets. The Airbus A320, for example, has a wing loading of around 610 kg/m2. This allows reasonably long range and high speeds, while still enabling acceptable takeoff and landing distances.
General aviation and trainer aircraft
Lower wing loading is desirable in many general aviation and trainer aircraft to improve low-speed handling and maximize safety. A larger wing area relative to the aircraft's weight allows slower takeoff and landing speeds, shorter runway requirements, and gentler stall characteristics.
The Cessna 172, one of the most popular trainers, has a wing loading around 14 lb/ft2 when lightly loaded. This relatively low value provides forgiving handling at typical general aviation speeds. In contrast, high performance aircraft like fighters may have wing loadings over 100 lb/ft2, trading docile low-speed behavior for agility and speed at the expense of longer takeoff rolls and higher stall speeds.
Gliders and ultralight aircraft
Gliders and ultralight aircraft are designed with extremely low wing loading to maximize lift and efficiency. These aircraft have large wing areas relative to their light weights, often with wing loadings below 10 kg/m². This allows them to generate sufficient lift at very low airspeeds.
The low stall speeds that result from minimal wing loading are critical for gliders, which lack an engine and must stay aloft by finding and circling in rising pockets of air called thermals. Ultralight aircraft also benefit from short takeoff and landing distances thanks to their low wing loading, enabling operation from small fields and remote areas. However, the tradeoff is that these aircraft are more susceptible to turbulence and crosswinds compared to heavier, faster planes with higher wing loadings.
In conclusion, wing loading is a critical parameter in aircraft design that impacts takeoff and landing distances, cruise speed and efficiency, and maneuverability. Designers must carefully balance wing loading for an aircraft's intended mission, with fighters prioritizing high wing loading for speed while general aviation favors lower values for shorter runways and gentler handling. Understanding this key concept allows optimizing designs and tailoring performance to specific roles, from efficient airliners to agile aerobatic planes. As in business, sometimes less is more - a lesson illustrated by the impressive short-field performance enabled by the low wing loadings of STOL aircraft.
Book a private flight
With Orizair, discover hundreds of available flights to reach your destination the green way.
Find your destinationAt Orizair, we integrate sustainability into private aviation by automatically offsetting the carbon emissions of every flight and collaborating with committed partners like Treesition. Discover our commitment.